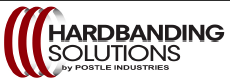
It’s All About the Chemistry
Each hardbanding product has its own, unique chemical composition, no two materials are the same. For example, some materials form Chrome Carbides or Titanium Carbides to provide wear resistance. The matrix which holds the carbides is also different for each product.
The chemistry of Duraband®NC was formulated to ensure that it can form a stable, 100% crack-free bond with the base material. Niobium is added to form niobium carbides which provide excellent wear resistance. Additional advantages of Niobium are that it has a low wear coefficient against casing and it remains stable without causing stress cracks even after several reapplications.
The exact chemistry of Duraband has remained unchanged and our secret for more than 16 years, when it was first used to protect the drill string.
Geothermal Versus Oil & Gas Drilling:
The Key Differences
-
Temperature: Geothermal wells often encounter higher temperatures
compared to oil and gas wells. This demands a hardbanding alloy
that can withstand these extreme conditions.
-
Torque and Drag Reduction: In the high-temperature environment
of geothermal wells, reducing torque and drag is crucial. The low
friction coefficient of Duraband®NC means we can minimize these
forces, ensuring smoother drilling operations.
-
Casing Protection: Given the longer lifespan and use of geothermal
wells to produce steam over years, protecting the casing from wear
during drilling is vital. Duraband®NC provides this protection,
extending the well’s operational life before remedial work would be
required.
-
100% Crack-Free Alloys: Stress-cracking in a hardband used in high
temperature and highly corrosive environments can lead to failure.
Hardbanding should be applied and reapplied 100% crack-free.